LiDAR (light detection and ranging) is a survey-mapping technology that detects objects and distances in 3D by measuring the time it takes for laser pulses to bounce off objects at a distance. Thermal management is crucial to most laser systems, and LiDAR lasers are no different. Stable temperatures within LiDAR systems are essential for optimal performance, as temperature fluctuations can lead to changes in laser wavelength and increased range errors. Excessive heat can degrade laser performance, reduce reliability, and even lead to component failure if not adequately managed. Depending on the system design, required power consumption, operating environment, and intended use, some LiDAR systems require enhanced active cooling solutions to maintain optimal and accurate performance.
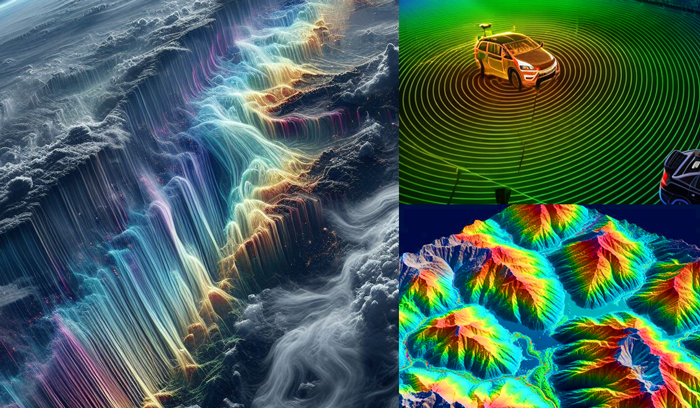
Lidar technology is used in a wide variety of applications. *AI generated image by Bing's Copilot
LiDAR System Components
LiDAR systems utilize laser diodes as the light source. Laser diodes generate a significant amount of heat during operation, especially if they are pulsed at high frequencies or operated at high power levels. Laser diode performance can quickly decline when temperatures go beyond the preferred operating temperature range, which is typically between 15°C to 35°C (59°F to 95°F) in LiDAR laser systems. Temperature changes can alter the laser wavelength, affecting output power, beam quality, spectral linewidth, and coherence length causing range errors, mode hopping and more.
Adding to thermal complexity, components including data acquisition units, signal processing circuits, and control systems also generate heat during operation. Efficient cooling solutions are essential to prevent overheating and ensure the reliable performance of these components.
LiDAR systems also feature sensitive optical components such as lenses, mirrors, and photodetectors. Thermal fluctuations can cause these components to expand or contract, leading to misalignment and affecting the accuracy of measurements. Active thermal stabilization techniques may be necessary to minimize these effects.
Cooling Requirements
LiDAR systems are often deployed in diverse environmental conditions, including extreme temperatures, humidity, and dust or debris. Cooling solutions must be robust enough to maintain optimal operating temperatures under varying environmental conditions without compromising system performance or reliability. Harsh environment applications include:
- Automotive
LiDAR used in autonomous vehicles or advanced driver-assistance systems (ADAS) are often mounted on vehicles exposed to varying environmental conditions. The heat generated by the lasers and associated electronics, combined with external factors such as sunlight, can lead to temperature fluctuations that affect the accuracy and reliability of the system. - Industrial
LiDAR components used in harsh manufacturing, mining, or forestry applications, generates enough heat that it becomes crucial to maintain optimal performance and prevent damage. - Aerospace and Defense
Unmanned aerial vehicles (UAVs), satellites, and military reconnaissance equipment face thermal challenges due to operating in high altitudes, rapid temperature changes, and potential exposure to intense radiation. - Atmospheric
LiDAR systems used for atmospheric research, meteorology, or environmental monitoring may operate in diverse climates and altitudes, where temperature differentials can affect the accuracy of measurements. Thermal management is essential to ensure precise data collection and instrument stability. - Long-range
LiDAR systems designed for long-range scanning, such as those used in topographic mapping, urban planning, or geological surveys, may require high-power lasers and sophisticated optics. Managing the heat generated by these components becomes critical for maintaining beam quality and avoiding thermal distortion.
Cooling Solutions
Many LiDAR system designers select thermoelectric coolers (TECs) for spot cooling on thermally sensitive components. In a LiDAR system, TECs can be mounted in direct contact with a laser diode. This allows for efficient heat transfer between the laser diode and the TEC. TECs absorb heat from the laser diode and pump it away, helping to maintain a stable operating temperature. If necessary, TECs are also placed near lenses, mirrors, and photodetectors to remove heat.
Thermoelectric coolers, also known as Peltier coolers, are rugged solid-state cooling devices that regulate the temperature of critical components despite the varying environmental conditions. Thermoelectric coolers offer a compact, lightweight, and energy-efficient cooling solution, enabling the reliable operation of the LiDAR system without the need for bulky external cooling equipment.
Tools like Laird Thermal Systems Thermal Wizard are available today to help design engineers quickly select the optimum thermoelectric cooler solution. If the Qc requirement is not known, the Laser Diode cooling calculator is a good place to start.
If your already know what you are looking for, select from the wide range of standard TEC solutions https://lairdthermal.com/products/thermoelectric-cooler-modules For custom requirements visit our prototyping solutions https://lairdthermal.com/thermal-design-services/prototyping/prototyping-thermoelectric-coolers
Conclusion
Designing LiDAR systems with efficient thermal dissipation characteristics can help mitigate thermal issues and enhance overall performance and reliability. TECs can be beneficial in a wide range of LiDAR applications where precise temperature control and compact, energy-efficient cooling solutions are required. TECs have low power requirements, are available in small and micro form factors, and maintain temperature stability of critical components, such as laser sources or optical assemblies, even in the harshest environments where traditional cooling methods may be impractical or unreliable.
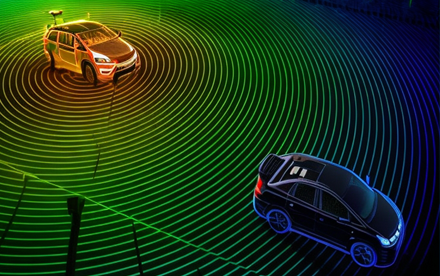
Related Products
Stay tuned for updates on thermal management industry regulations, new product releases, and innovative temperature control approaches with
LTS Thermal Solutions Spotlight:
Categories
Blog Date