Peltier Cooling for Digital Light Processors
Introduction
Digital light processors employ a laser light source and millions of tiny mirrors to produce vibrant, high-resolution images for a wide variety of industries and applications. It is critical to maintain an optimum operating temperature during use to prevent degradation of the digital light processing technology. Active cooling solutions utilizing thermoelectric coolers can provide digital light processors thermal management in a wide range of high temperature applications.
Background
Digital light processing technology is based on optical micro-electro-mechanical systems (MEMS) technology. It uses a grid of microscopic, highly-reflective aluminum mirrors placed on a semiconductor chip known as a digital micromirror device (DMD). The DMD receives electrical input through electronic control units (ECU) individually positioned adjacent to each micromirror and produces optical output via spatial light distribution. Separate control of each micromirror optimizes performance, resulting in a highly efficient, reliable, and high-speed device. A digital light processor chip uses millions of micromirrors to project sharp, crisp images with extremely high feature resolution and vibrant colors. The technology works with a variety of light sources, including high-powered LEDs and lasers, depending on the specific application.
Digital light processing technology is used in the following three major applications:
Automotive
The automotive industry uses digital light processors in smart headlights and head-up displays (HUD). Smart headlights automatically manage the direction of the high beams, adjusting them away from oncoming traffic or into the direction of a turn so they illuminate and enhance the driver’s viewable area. The light from smart headlights travels farther, providing a longer viewpoint and more time for the driver to safely respond to hazards ahead. Head-up displays project images, which may include travel speed or directions from a GPS system, onto the windshield within the driver’s field of view. This allows the driver to remain focused on the road ahead rather than looking down at the dashboard. An additional safety feature in HUD may be enhanced signage recognition with display on the windshield.

Heads-up displays project images on the windshield such as travel speed or directions from a GPS system.
Display and projection
In display and projection applications, digital light processing technology uses two chip sizes. Pico chipsets are used for compact and ultra-mobile applications, delivering excellent image quality for devices including smartphones, tablets, virtual and augmented reality headsets and glasses, gaming accessories, medical devices, and elevator signage. Smart home applications such as thermostats, lighting, appliance displays, and entertainment systems can also operate using these pico chipsets. Larger displays use standard chipsets and include applications such as laser TVs, large-scale digital signage in airports and sporting arenas, and educational tools like classroom multimedia devices where vivid, high-resolution images are needed.
Advanced light control
The third application is advanced light control, where digital light processing technology offers high-resolution light patterns, extremely fast pattern rates, and highly reliable pixel control. Stereolithographic 3D printing is an additive-manufacturing technique in which material is deposited, one layer at a time, to build an object; digital light processing technology exposes each complete layer to light to cure the photosensitive polymers. Digital lithography, used in the manufacture of printed circuit boards, relies on digital light processing to expose the photosensitive materials without the need for contact masking. Spectroscopic analysis units can use digital light processor chips as wavelength selectors, eliminating the need for a linear-array detector and improving the efficiency of the chemical analysis. Additional applications exist in the medical, food, and agricultural arenas. Digital light processors are available in light wavelengths in the visible, ultraviolet, and near-infrared spectrums, depending on the specific application.

Stereolithographic 3D printing utilizes digital light processors in the ultraviolet and near-infrared spectrum.
Thermal Challenges
Design engineers can experience a variety of thermal challenges when implementing digital light processing technology, including thermal noise, SWaP (size, weight, and power) constraints, lack of airflow, and outgassing. These systems also inherently generate heat during operation that needs to be efficiently dissipated to maintain proper operation.
Digital light processor systems utilize a highly temperature-sensitive semiconductor chip as the base for the DMD. DMD systems operate efficiently from 0 – 70°C. DMD performance is extremely robust over this relatively large operating temperature range. However, there is a direct correlation between extreme temperature conditions and performance degradation. As a result, operating and storage temperature limits are imposed on DMDs.
Some digital light processor applications operate in high-heat environments. For example, temperatures in smart headlights can reach as high as 110°C due to a combination of external environmental conditions: heat generated by the engine, adjacent electronics, and heat generated by the digital light processor itself. In addition, many applications require packing more electronics into compact spaces to meet size and functional requirements, which further increases the heat flux density and makes it difficult to get the heat out. For example, the more information a HUD unit displays, the higher power it requires. A higher-powered unit will generate more heat, raising the operating temperature of the system.
In addition to operating in tight spaces, automotive and consumer electronics need to be lighter and more efficient, which requires a cooling solution that is just as compact and efficient. Space constraints can negatively impact airflow, resulting in reduced performance of the thermal management solution such as heat sinks. This is often found in compact smart headlight compartments where air does not always flow consistently in one direction, lowering the effect of the heat sink. Constant airflow ensures proper heat dissipation, as does proper selection of a thermal solution that accounts for all application variables.
Additionally, it is important to consider environmental issues. In digital light processor applications, outgassing must be avoided as it can coat the device or laser optics and degrade performance over time. Creating protective housing to prevent moisture, condensation, and the ingress of other outside contaminants is critical in order to protect sensitive electronics.
Thermal Solutions
There are two methods for heat dissipation in digital light processor components. Passive cooling using thermal interface materials and heat sinks is an efficient process that uses conduction to dissipate thermal energy. Passive cooling systems have no moving parts, making them ultra-reliable. However, they cannot cool below ambient temperature, which can be a problem at higher temperatures. Active thermoelectric cooling, on the other hand, uses a thermoelectric cooler and a heat sink with a fan or blower to provide efficient spot cooling, which keeps the system safely within its specified operating temperature range to ensure peak performance and image quality.
Active cooling systems—like thermoelectric coolers—manage the heat-sensitive DMD’s temperature by creating a temperature differential. A thermoelectric cooler can lower the temperature by as much as 50°C from the hot-side temperature of the heat exchanger. The thermoelectric cooler can be installed so that it comes in direct contact with the digital light processor, or a cold block can be created. When power is applied to the thermoelectric cooler it absorbs heat from the device and pumps it thru the cooler into a hot side heat dissipation mechanism, which typically is a heat sink and fan. It is important to ensure that the hot-side heat sink does not saturate, which would allow heat to flow back into the device. Optimizing the thermoelectric cooler for a high coefficient of performance (COP) is critical, however. Temperature sensing with closed-loop feedback and control may be necessary as well. Even though Peltier cooling modules cost more than passive cooling, they are necessary in high temperature applications.
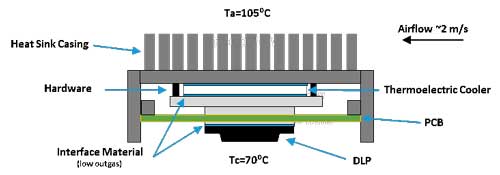
2-D diagram of cooling digital light processing application
Tark Thermal Solutions DLP applications
Laird Thermal Systems has expertise in designing and implementing Peltier thermal management solutions, with proficiency in mating heat exchangers to maximize heat transfer most efficiently, no matter the airflow characteristics. Laird Thermal Systems offers both standard and custom design solutions to eliminate thermal noise and meet application SWaP (size, weight, and power) requirements. The modules offer reliable solid-state construction, long life operation and a compact form factor that fits into most DLP applications. Thermoelectric coolers also eliminate outgassing, as the proprietary thermal interface materials feature extremely low outgas properties.
OptoTEC™ OTX/HTX Thermoelectric Coolers
Available in a footprint as small as 3 X 4 mm the OptoTEC™ OTX/HTX Series is designed to fit space constrained applications such as digital light processors. Offering up to 10 Watts of cooling power, this product series provide superior heat pumping capacity in an extremely small form factor. Featuring next generation materials, the OptoTEC OTX/HTX Series boosts cooling performance over standard product offerings while offering a higher coefficient of performance (COP).
The OptoTEC Series is available in OTX and HTX versions. The OptoTEC OTX uses SbSn solder, enabling a maximum operating temperature of 120°C and a melting point of 232°C for reflow purposes. The OptoTEC HTX thermoelectric cooler utilizes AuSn solder that allows it to operate in temperatures up to 150°C with a melting point of 280°C.
OptoTEC OTX/HTX thermoelectric coolers have passed Telcordia GR-468 CORE requirements to withstand harsh operating environments.

The OptoTEC™ OTX/HTX Series comes in an extremely small form factor offering up to 10 Watts of cooling power.
HiTemp ETX Thermoelectric Coolers
The HiTemp ETX Series thermoelectric coolers are designed for applications where the ambient temperature exceeds the maximum operating temperature of the sensitive electronics requiring cooling. The thermoelectric cooler features an enhanced module construction that prevents performance-degradation, which is common in standard-grade thermoelectric coolers operating in temperature environments exceeding 80°C. The HiTemp ETX Series protects critical electronic components in digital light processors and provides active cooling for applications operating in temperatures ranging from 80°C to 150°C with precise temperature control up to 0.01°C. Compared to standard thermoelectric coolers, this product series features advanced thermoelectric materials, boosting cooling capacity by up to 10%. The improved thermal insulating barrier creates a maximum temperature differential (ΔT) of 83°C.
The HiTemp ETX Series is available in more than 50 models with a wide range of heat-pumping capacities, geometric form factors, and various input voltages to cover the wide range of DLP design requirements. Heat pumping capacities range from 7.7 to 340 Watts in form factors as small as 12 mm x 12 mm to 62 x 62 mm.

HiTemp ETX Series is offered in more than 50 models with a wide range of heat-pumping capacities, form factors and various input voltages
Thermal Wizard Product Specification and Selection Tool
Selecting the right thermal solution for a particular application can be a long and difficult process for a thermal engineer, one that requires many technological and financial trade-offs. In order to speed-up and simplify this process, Tark Thermal Solutions developed the Thermal Wizard™ to serve as a virtual thermal management assistant so that thermal decisions can be made faster and more accurately. The Thermal Wizard does the heavy lifting, sorting through the data and calculating the performance, leaving the decisions to the designer. The Thermal Wizard simulates cooling applications to help select thermoelectric coolers, thermoelectric cooler assemblies, or liquid cooling systems. The Thermal Wizard is available at https://tark-solutions.com/thermal-wizard/qc-cooling-selector-home
Conclusion
DLP technology is used for applications ranging from smart automotive headlights and vehicle head-up displays to projection and advanced light control. Heat fluctuations within the devices can lead to degradation of performance, loss of accuracy, and reduced image resolution. Use of active cooling solutions with HiTemp ETX Series thermoelectric coolers can provide the necessary protection to keep sensitive electronics below their maximum operation temperatures. Tark Thermal Solutions offers both standard and custom design solutions that meet DLP technology requirements.
Visit our website to find OptoTEC OTX/HTX Series or HiTemp ETX Series
